- 1.1. Block Flow Diagram (BFD)
- 1.2. Process Flow Diagram (PFD)
- 1.3. Piping and Instrumentation Diagram (P&ID)
- 1.4. Additional Diagrams
- 1.5. Three-Dimensional Representation of a Process
- 1.6. The 3-D Plant Model
- 1.7. Operator and 3-D Immersive Training Simulators
- 1.8. Summary
- References
- Short Answer Questions
- Problems
1.7. Operator and 3-D Immersive Training Simulators
1.7.1. Operator Training Simulators (OTS)
Up to this point in the chapter, the different elements and diagrams used in the specification and description of a process have been covered. The means by which the material balances, energy balances, and design calculations for the various unit operations, required to specify all the design conditions, have been carried out has not been covered. Indeed, the simulation of chemical processes using programs such as CHEMCAD, Aspen Plus, PRO/II, HYSIS, and others is not addressed until much later, in Chapter 13. Nevertheless, it should be clear that extensive simulation of the process will be required to determine and to specify all of the conditions needed in the design. Typically, these simulations are carried out under steady-state conditions and represent a single design operating point, or possibly are made for several different operating points. The steady-state simulation of the process is clearly very important from the standpoint of defining the design conditions and specifying the equipment parameters, such as vessel sizes, heat-exchanger areas and duties, pipe sizes, and so on. However, once the plant has been built, started up, and commissioned, it is rare that the process will operate at that design condition for any given period of time. Moreover, how the process can be started up or run at, for example, 65% or 110% of design capacity is not evident from the original design. Nevertheless, the plant will be run at off-design conditions throughout its life. In order to help operators and engineers understand how to start up and shut down the process, deal with emergencies, or operate at off-design conditions, an operator training simulator (OTS) may be built.
The foundation of an OTS is a dynamic simulation (model) of the process to which a human machine interface (HMI) is connected. The HMI, in its simplest form, is a pictorial representation of the process that communicates with the dynamic model, and through it, process variables are displayed. The HMI also displays all the controls for the process; an operator can control the process by changing these controls. An example of an HMI is shown in Figure 1.16. This particular example shows a portion of an acid-gas recovery (AGR) unit for an OTS developed by the Department of Energy to simulate an IGCC (Integrated Gasification Combined Cycle) coal-fed power plant. Process variables calculated by the dynamic model are displayed in boxes throughout the HMI. Operators can monitor the change in these variables with time just as they would in a control room situation. The only difference is that the process is simulated rather than actually operating. In general terms, the OTS functions for an operator just as a flight simulator does for a pilot or astronaut. Therefore, operators and engineers can gain operational experience and understanding about a process or plant through the OTS but with the added benefit that any mistakes or errors can be identified and corrected during training sessions without exposing personnel to any risks that might occur if training were to be done on the actual plant.
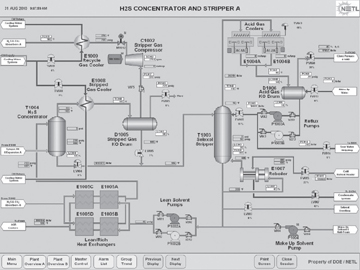
Figure 1.16. Example of an HMI Interface for an OTS (Reproduced by Permission of the DOE’s National Energy Technical Laboratory and Invensys Systems Inc., Property and Copyright of Invensys plc, UK)
The starting point for developing an OTS is the steady-state simulation, the equipment information, and instrumentation and control data. In general, the P&IDs are used as the starting point for the generation of the HMI since they contain all the necessary information for the controls and instrumentation. The dynamic model is developed so that the steady-state design condition will be simulated when all the inputs (feeds) are at their design values. Details of how dynamic simulators are used in process design are included in Chapter 17. Needless to say, the development of a fully functioning dynamic model for a process that accurately reflects all the controls and valves in the process is a substantial task that takes a team of engineers many months to accomplish.
1.7.2. 3-D Immersive Training Simulators (ITS)
In Section 1.6, the concept of a 3-D plant model was introduced. Such models are “constructed” in an “electronic” environment using precise design data on the size, location and elevation (x-, y-, and z-coordinates), and orientation of each piece of equipment. In addition, the piping arrangement and location of valves, nozzles, instruments, sample ports, drains, and so forth are all specified. Such a representation allows the engineer and operator to evaluate the accessibility of critical process components and to obtain a feel for how the plant will look (and operate) when constructed. The engineer may access this information through either a 2-D viewer or a 3-D virtual environment (for example, using 3-D goggles). However, no matter how the information is viewed, the resulting images are essentially static and are generally of low to medium fidelity. Therefore, when viewing a 3-D plant model, it will always be clear to the viewer that it is just a model, and that the representation of the 3-D object is crude.
The visual enhancement of 3-D models using sophisticated imaging software and overlaying photorealistic images on top of a skeleton of the 3-D representation are now not only possible but commonplace for higher-end video games. Computer-generated graphics are now so advanced that, as any movie fan will attest, it is often difficult to determine what is “real” and what is animated. This technology is now being applied to develop 3-D immersive training simulators (ITS) for chemical plants. As can be seen from Figure 1.17, the quality and realism captured by computer-generated graphics are truly amazing. Furthermore, the use of avatars to represent plant operators makes it possible for a user to navigate through, interact with, and be truly immersed in the virtual plant.

Figure 1.17. An Example of a Computer-Generated Image of a Horizontal Drum (Reproduced by Permission of the DOE’s National Energy Technical Laboratory and Invensys Systems Inc., Property and Copyright of Invensys plc, UK)
1.7.3. Linking the ITS with an OTS
The potential for education and training of engineers, operators, and students using both the OTS and ITS appears to be limitless. Indeed, these two systems can be linked together such that they can communicate, and the real-time operation of the process, both in the control room and outside in the plant, can be simulated in the virtual environment. Consider the following scenario that might occur during the start-up of a chemical process:
- Feed to a distillation column from an on-site storage drum has begun. The feed pump has been started and the flow through the pump has been confirmed from the HMI display in the control room. The liquid feed flows into the top of the tower, and the liquid levels on the distillation trays start to increase. The process appears to be working as described in the start-up manual that the operator is following. However, approximately 30 minutes after the start of the feed pumps, a low-level alarm sounds on the on-site storage drum. The operator monitors the level in the drum from the control room and determines that it is continuing to fall and will cause the feed pump to vapor lock (cavitate) if the situation is not remedied. In reviewing the start-up procedure, the operator determines that there is a remote function valve (one that cannot be operated remotely from the control room) that connects the on-site storage drum to the off-site storage tank, and that this valve may have been closed inadvertently. She then contacts an operator in the field by walkie-talkie and asks him to check the status of the remote function valve. The field operator walks to the storage drum, identifies the tag name on the valve, and confirms that the valve is indeed closed. The control room operator then instructs the field operator to open the valve, which he does. The control room operator then confirms that the level in the drum has started to go back up and thanks the field operator for his help.
This scenario might well represent an actual incident during a scheduled plant start-up. However, this scenario could just as easily be simulated in the virtual environment. The control room operator would be sitting in front of the HMI screen that is connected to the OTS. A field operator could be sitting in the room next door with a walkie-talkie and wearing 3-D goggles connected to the ITS. The field operator would move his avatar to the location of the on-site storage drum and locate the remote function valve. The field operator using his avatar would then note the setting of the valve and after receiving instructions from the control room operator would open the valve. At this point, the ITS would communicate to the OTS that a valve had been opened, and this would then allow the flow of product to continue to the drum; that is, the dynamic model of the process would respond to the valve being opened and model the flow to the drum. The control room operator, monitoring the HMI, would see the result of the flow of product as an increase in the drum level.
Clearly, any number of scenarios involving control room operators and field operators could be implemented. Moreover, maintenance operations, safety training, and a whole host of other operator functions could be simulated-all in the virtual plant.
Augmented Reality. From the previous example it is clear that any feasible scenario that might occur in the actual plant can be simulated in the virtual environment. However, a series of cases can be simulated that would be almost impossible to simulate in the actual plant but are easily accomplished in virtual reality. For example, it might be helpful to show a young engineer how a particular piece of equipment works by showing him or her the details of the internals of that equipment. In the actual plant, this opportunity might not be available until a scheduled plant shutdown occurs, and that might not happen for one or two years. However, in the virtual environment, the operation of a given piece of equipment can be easily displayed. In fact, the avatar can move into the plant and simply “strip away” the outer wall of a piece of equipment and look inside to see what is happening. This additional feature is sometimes referred to as augmented reality (AR). As an example of AR, the operation of a reboiler and a distillation column is illustrated in Figures 1.18(a) and 1.18(b), respectively.
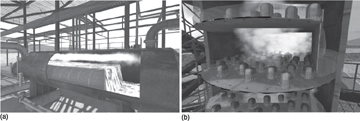
Figure 1.18. Augmented Reality in ITS: (a) Reboiler (b) Bubble-Cap Distillation Column (Reproduced by Permission of the DOE’s National Energy Technical Laboratory and Invensys Systems Inc., Property and Copyright of Invensys plc, UK)
Another example of AR is the display of process data in the virtual plant. For example, if an operator wanted to check on the trend of a certain process variable, say, the temperature in a reactor, or look at a schematic of a pump, the avatar can simply click on a piece of equipment and display that trend, as shown in Figure 1.19. Clearly, in the virtual environment, there are very few limitations on what information the operator (avatar) can access.
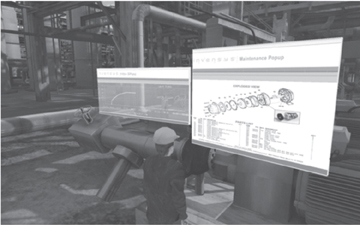
Figure 1.19. An Avatar Can Access Process Trends and Observe Equipment Schematics in AR (Reproduced by Permission of Invensys Systems Inc., Property and Copyright of Invensys plc, UK)
Training for Emergencies, Safety, and Maintenance. The possibilities for training operators and engineers in the virtual plant environment are unlimited. Of particular importance are the areas of safety, emergency response, and routine maintenance. For example, the response of an operator or team of operators to an emergency situation can be monitored, recorded, and played back in the virtual plant. Any mistakes made by the operator(s) can be analyzed, feedback given, and then the exercise can be repeated until the correct response is achieved. Although such training does not absolutely guarantee that when a real emergency arises in the plant the operators will respond correctly, it nevertheless provides crucial emergency training under realistic conditions without the fear of actual harm to personnel and equipment. Furthermore, the more often such scenarios are rehearsed, the more likely are operators to respond correctly when real emergencies occur in the plant.
Corresponding scenarios for safety and maintenance training can also be implemented. Often these activities must follow well-defined procedures, and again, the virtual environment offers a perfect venue to record, analyze, and provide feedback to personnel as they perform these various tasks.
In summary, the use of the virtual plant environment (ITS linked to an OTS) provides unlimited opportunities to a new generation of engineers and operators to learn and to train as process plant personnel and to hone their respective skills in an environment that is both realistic and safe.